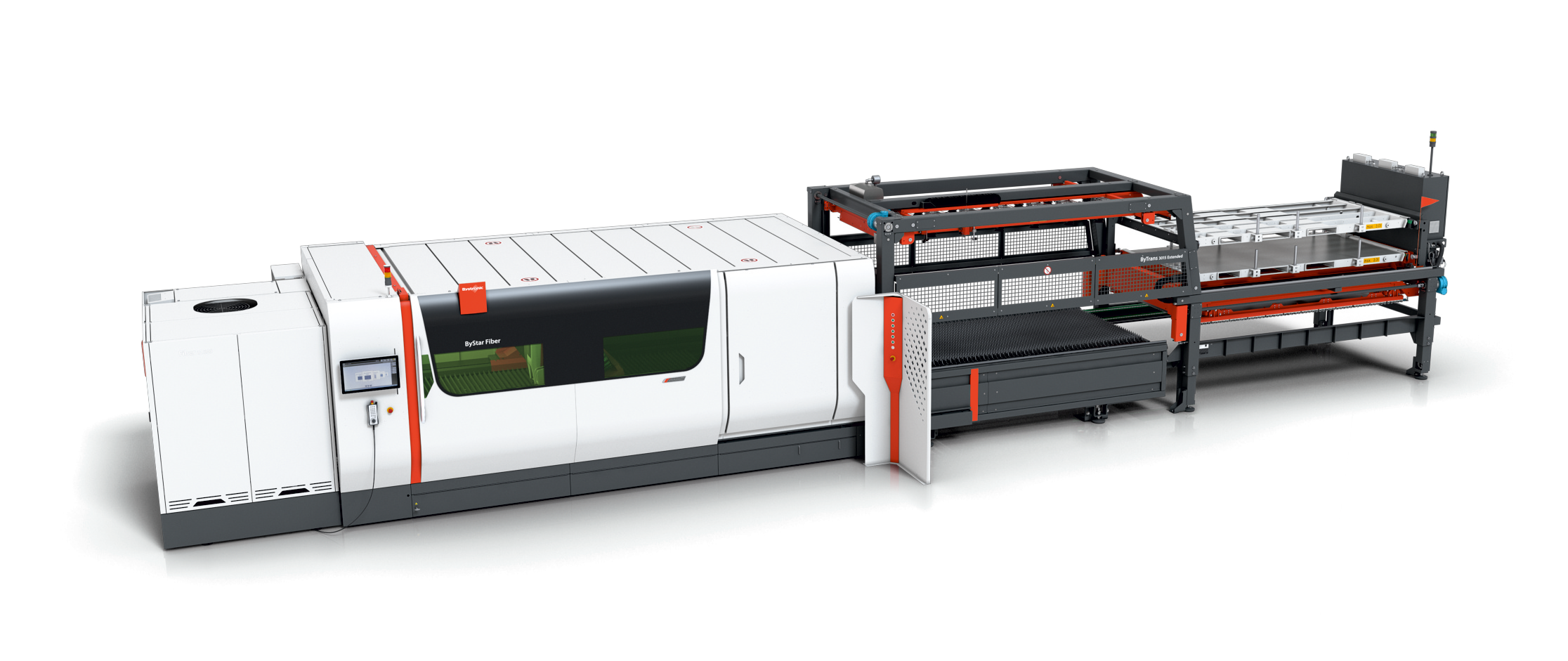
The Precision Services Department provide....
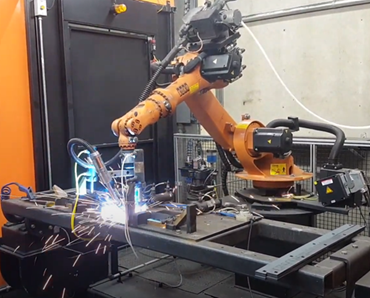
Advantages of Robotic Welding
- Increased productivity : robots can weld 3-5x faster than humans
- Repeatable and consistent: a robotic welder can perform the same weld cycle for 24 hours, 7 days a week.
- Safety: reduced accidents to workers
- Quality: robotic welders can achieve superior quality by ensuring the correct angle, speed and distance
Our large on-site store of different grade of steel materials allows us to quickly perform any work we need to, and deliver your parts on schedule, every time.
With over 80,000 square feet of production area, we have the capabilities to take on any project big or small.
We can bend sheet and plate products to different degrees using a press brake and other bending techniques.
The brake (hydraulic or manual) creates bends by clamping the metal piece in between an upper and lower die. These bends can be made up to an angle of 120 degrees. Using press brakes is considered to be an accurate and extremely fast method of bending metal.
Typically core shapes can be produced either by pressing and firing or machining the shape from a block of material. Pressing requires special tooling for each shape which can cost many thousands of dollars depending on the complexity of the design. Designs with low forecasted volume requirements can be machined avoiding the high capital tooling expenditures.
For those products that have high volumes forecasted it is always best to prove the designs using a machined part so that press tooling may be made just once at the final design stage. Please contact our engineers to discuss your custom core design needs.
CUSTOM MACHINING CAPABILITIES
- Four-axis CNC’s for special contours, profiles and shapes
- Abundant ID/OD/Centerless and surface grinding capacity
- Lapping and Polishing as fine as six micro-inch surface finish
- High quality assembly and bonding techniques
- Parylene coating